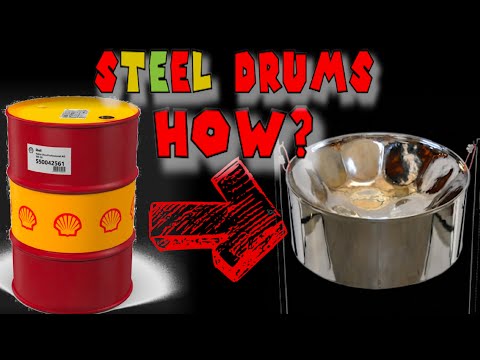
콘텐츠
- TL; DR (너무 길고 읽지 않음)
- 튜브 제조 공정에서 용접 대 원활한 생산
- 용접 및 심리스 스틸 튜브에 대한 단계별 엔지니어링 프로세스
- 잉곳, 블룸, 슬래브 및 빌렛 생성
- 파이프로이 재료 제작
- 용접 및 이음매없는 파이프 개발
- 추가 처리 및 아연 도금
- 파이프 제조의 역사
- 강관의 힘
철, 알루미늄, 탄소, 망간, 티타늄, 바나듐 및 지르코늄을 포함한 원자재로 제작 된 스틸 튜브는 난방 및 배관 시스템, 고속도로 공학, 자동차 제조 및 심지어 의학 (수술 용 임플란트 및 심장 판막 용)에 이르는 파이프 생산의 중심입니다. .
개발이 1800 년대에 시작된 혁신적인 기술로 거슬러 올라 가면서, 건축 방식은 다양한 목적에 따라 다양한 디자인에 적합합니다.
TL; DR (너무 길고 읽지 않음)
스틸 튜브는 용접 또는 다양한 목적을위한 완벽한 프로세스를 사용하여 구성 할 수 있습니다. 수세기에 걸쳐 수행 된 튜브 제조 공정은 원료부터 의약품, 제조에 이르기까지 역사에 응용되어 온 완제품에 이르기까지 다양한 단계를 거쳐 알루미늄에서 지르코늄에 이르는 재료를 사용합니다.
튜브 제조 공정에서 용접 대 원활한 생산
자동차 제조에서 가스 파이프에 이르기까지 강관은 합금 (다른 화학 원소로 만든 금속)으로 용접하거나 용해로에서 완벽하게 구성 할 수 있습니다.
용접 튜브는 가열 및 냉각과 같은 방법을 통해 강제로 연결되고 배관 및 가스 운송과 같이 더 튼튼하고 더 단단한 용도에 사용되는 반면, 이음매없는 튜브는 자전거 및 액체 운송과 같은보다 가볍고 얇은 목적을 위해 신축 및 중공을 통해 생성됩니다.
생산 방법은 강관의 다양한 디자인에 적합합니다. 직경과 두께를 변경하면 가스 수송 파이프 라인과 같은 대규모 프로젝트와 피하 주사 바늘과 같은 정밀 기기의 강도와 유연성에 차이가 생길 수 있습니다.
튜브의 폐쇄 구조는 원형, 정사각형 또는 모양에 관계없이 액체의 흐름에서 부식 방지에 이르기까지 필요한 응용 분야에 적합합니다.
용접 및 심리스 스틸 튜브에 대한 단계별 엔지니어링 프로세스
강관을 만드는 전체 과정에는 원료 강을 잉곳, 블룸, 슬래브 및 빌릿 (모두 용접 할 수있는 재료)으로 변환하여 생산 라인에 파이프 라인을 만들고 파이프를 원하는 제품으로 만드는 과정이 포함됩니다.
••• Syed Hussain Ather잉곳, 블룸, 슬래브 및 빌렛 생성
가열 된 석탄에서 탄소가 풍부한 물질 인 철광석과 코크스는 용광로에서 액체 물질로 녹은 다음 산소로 분사되어 용강을 만듭니다. 이 재료는 대량의 압력 하에서 롤러 사이에 형성되는 재료를 저장 및 운반하기위한 강의 주물 인 잉곳으로 냉각된다.
일부 잉곳은 강철 롤러를 통과하여 얇고 긴 조각으로 뻗어 강철과 철 사이에 꽃이 핀다. 또한 슬래브의 모양을 자르는 쌓인 롤러를 통해 직사각형 단면의 강철 조각 인 슬래브로 롤링됩니다.
파이프로이 재료 제작
코인으로 알려진 프로세스 인 더 많은 롤링 장치가 빌렛으로 생깁니다. 이들은 원형 또는 정사각형 단면을 가진 금속 조각으로 더 길고 얇습니다. 플라잉 시어는 빌렛을 정확한 위치에서 절단하여 빌렛을 쌓아 심리스 파이프로 만들 수 있습니다.
슬라브는 가단성이 될 때까지 화씨 약 2,200도 (섭씨 1,204도)까지 가열 된 다음, 껍데기로 얇아지며, 이는 최대 0.25 마일 (0.4km) 길이의 좁은 리본 스트립입니다. 그런 다음 황산 탱크를 사용하여 냉수 및 온수를 사용하여 강을 청소하고 파이프 제조 공장으로 운송합니다.
용접 및 이음매없는 파이프 개발
용접 파이프의 경우 풀기 기계는 스 켈프를 풀고 롤러를 통과하여 가장자리가 말려 파이프 모양을 만듭니다. 용접 전극은 고압 롤러가 조이기 전에 전류를 사용하여 끝을 함께 밀봉합니다. 이 공정은 분당 1,100 피트 (335.3m)의 속도로 파이프를 생산할 수 있습니다.
이음매없는 파이프의 경우 정사각형 빌렛을 가열하고 고압으로 압연하는 과정에서 중심에 구멍이 생깁니다. 압연기는 원하는 두께와 모양으로 파이프를 뚫습니다.
추가 처리 및 아연 도금
추가 처리에는 교정, 나사산 가공 (파이프 끝단에 단단한 홈을 절단) 또는 녹 방지를 위해 아연 또는 아연 도금 보호 오일 (또는 파이프 목적에 필요한 모든 것)을 포함 할 수 있습니다. 아연 도금은 일반적으로 소금물과 같은 부식성 물질로부터 금속을 보호하기 위해 아연 코팅의 전기 화학 및 전착 공정을 포함합니다.
이 과정은 물과 공기에서 유해한 산화제를 막는 역할을합니다. 아연은 산화 아연을 형성하기 위해 산소에 대한 애노드 역할을하며, 물과 반응하여 수산화 아연을 형성한다. 이러한 수산화 아연 분자는 이산화탄소에 노출 될 때 탄산 아연을 형성한다. 마지막으로, 탄산염의 얇고 뚫을 수없는 불용성 층은 금속을 보호하기 위해 아연에 달라 붙습니다.
더 얇은 형태의 전기 아연 도금은 일반적으로 용융-방지 페인트가 필요한 자동차 부품에 사용되며, 그에 따라 용융액이 모재의 강도를 감소시킨다. 스테인레스 스틸은 스테인레스 부품이 탄소강으로 아연 도금 될 때 생성됩니다.
파이프 제조의 역사
••• Syed Hussain Ather용접 된 강관은 1815 년에 석탄 가스를 수송하기 위해 머스킷의 배럴로 만들어진 석탄 연소 램프 시스템에 대한 스코틀랜드 엔지니어 윌리엄 머독 스 (William Murdocks)의 발명품으로 거슬러 올라가는 반면, 1880 년대 후반까지 휘발유와 석유를 수송하기 위해 이음매없는 파이프가 도입되지 않았습니다.
19 세기에 엔지니어들은 1824 년에 가열 될 수있을 때까지 가열 된 평평한 철제 스트립을 접는 방식으로 접는 망치를 사용하는 엔지니어 제임스 러셀 (James Russells) 방법을 포함하여 파이프 제작의 혁신을 만들었습니다.
내년 엔지니어 코메니우스 화이트 하우스는 파이프에 말려서 용접 된 얇은 철판을 가열하는 더 나은 맞대기 용접 방법을 만들었습니다. Whitehouse는 원뿔 모양의 개구부를 사용하여 가장자리를 파이프 모양으로 말아서 파이프에 용접했습니다.
이 기술은 자동차 제조 산업 내에서도 널리 사용되며, 구부러진 튜브 제품을보다 효과적으로 생산하기위한 열 성형 튜브 엘보우와 같은 새로운 돌파구를 통해 석유 및 가스 수송에 사용되며 지속적인 튜브 형성은 일정한 흐름을 유지합니다.
1886 년 독일 엔지니어 인 Reinhard와 Max Mannesmann은 Remscheid에있는 아버지 파일 공장에서 다양한 부품으로 이음매없는 튜브를 만드는 최초의 롤링 프로세스를 특허했습니다. 듀오는 1890 년대에 강철 튜브의 직경과 벽 두께를 줄여 내구성을 높이기위한 방법 인 필거 롤링 공정을 발명했습니다.이 기술은 다른 기술과 함께 강철 튜브의 분야를 혁신하기 위해 "Mannesmann 공정"을 형성합니다. 공학.
1960 년대 CNC (Computer Numerical Control) 기술을 통해 엔지니어는보다 복잡한 설계, 더 단단한 굴곡 및 더 얇은 벽을 위해 컴퓨터 설계 맵을 사용하여보다 정확한 결과를 얻기 위해 고주파 유도 형 기계를 사용할 수 있습니다. 컴퓨터 지원 설계 소프트웨어는 훨씬 더 정밀하게 현장을 계속 지배 할 것입니다.
강관의 힘
강철 파이프 라인은 일반적으로 수백 년 동안 지속될 수 있으며 천연 가스와 오염 물질의 균열뿐만 아니라 메탄과 수소에 대한 낮은 투과율의 영향에도 견딜 수 있습니다. 폴리 우레탄 폼 (PU)으로 단열하여 열 에너지를 보존하면서 강하게 유지할 수 있습니다.
품질 관리 전략은 x- 레이를 사용하여 파이프의 크기를 측정하고 관찰 된 편차 또는 차이에 따라 적절히 조정하는 등의 방법을 사용할 수 있습니다. 따라서 파이프 라인이 고온 또는 습한 환경에서도 적용에 적합합니다.